The Early Years: Wright Brothers to Amelia Earhart
On Dec. 17, 1903, Orville and Wilbur Wright completed the first-ever controlled heavier-than-air powered flight in Kitty Hawk, NC. The brothers used very simple materials to construct their aircraft, including:
- Spruce and ash for the frame
- Wheels from roller skates for pulleys
- Waxed twine to support the frame
- Cotton muslin for wing coverings
- Steel rods and sheets for control cables and strapping
Despite efforts to ensure quality control and airplane safety, the wood and fabric used in the first aircraft did not stand up well to the elements and needed to be replaced frequently.
By 1912, some aircraft manufacturers were constructing laminated wooden fuselages using monocoque construction, meaning weight is supported using the external skin of the fuselage, similar to an eggshell. This type of construction makes load-carrying internal frames unnecessary. World War I era German Albatros fighters and the Lockheed Vega used by Amelia Earhart were made in this style.
At this point, plane interiors were designed more for functionality than comfort. Most aircraft were used for transporting cargo or military applications, not passenger travel. Seats were often made of wicker in the earliest planes, and the interiors were sparse.
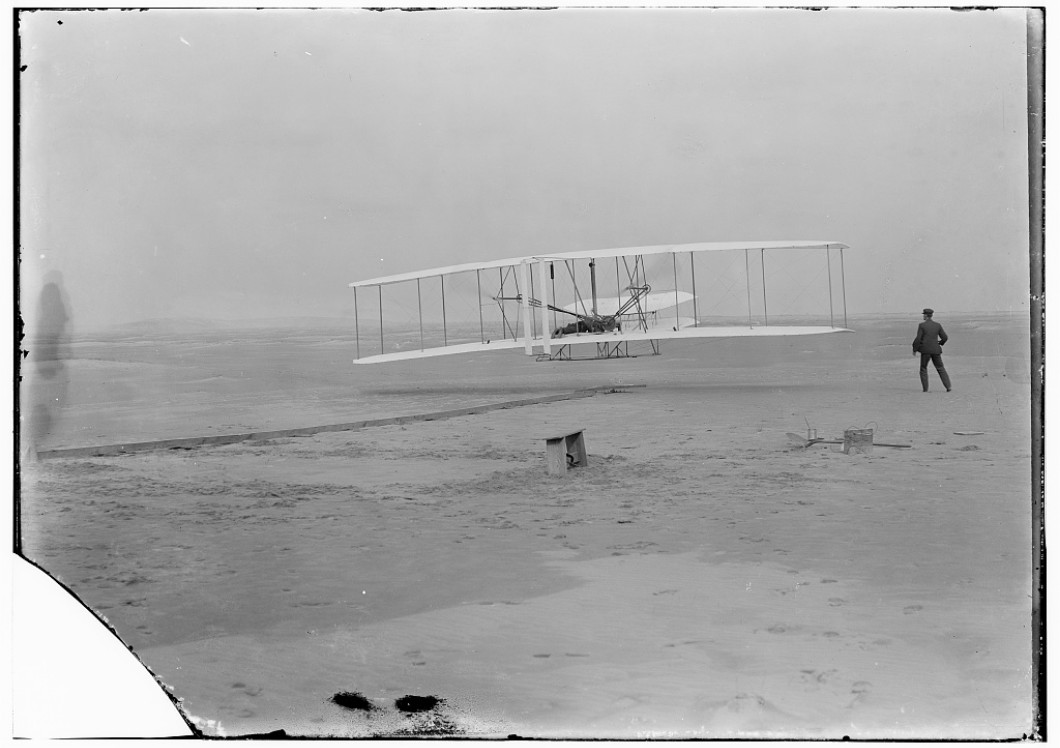
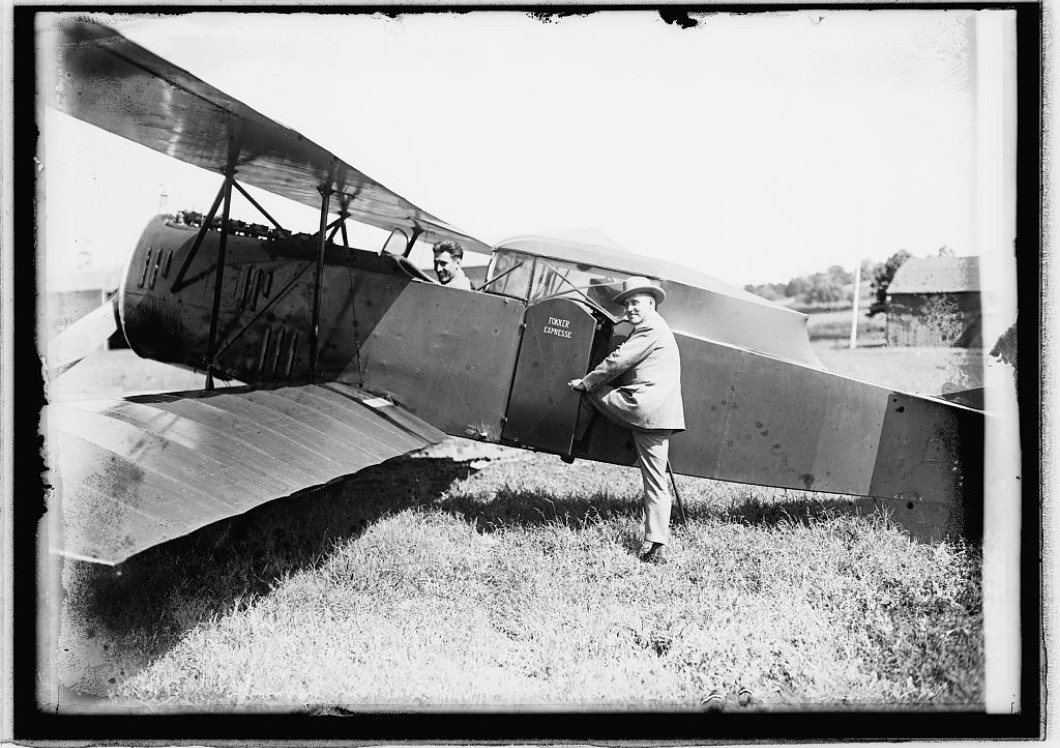
World War I to World War II: All-Metal Airplanes
As planes began to go faster in the next phase of airplane evolution, engineers started experimenting with using metal to ensure the aircraft were strong enough to withstand the wind resistance and other forces placed on the plane.
One of the most well-known metal airplanes were the Fokkers used in World War I, which were manufactured using fuselages made of welded steel tube.
From 1919 to 1934, all-metal airplanes were more common than wood aircraft. The strength and durability of metal allowed manufacturers to create airplanes that were lighter and easier to create and repair than wooden aircraft. Some of the most common types of construction methods were aluminum with surfaces covered in fabric or the all-metal monocoque aircraft.
Although all-metal planes were an improvement over wood, they still faced challenges, such as metal fatigue and corrosion.
After World War II, American and British scientists were exploring the possibilities of high-speed aviation. This research led to experimental supersonic aircraft, which required high levels of strength and thermal resistance. Aluminum alloys and exotic materials were used to meet these challenges. Planes were manufactured using:
- Silicon carbide ceramic coatings
- Titanium alloys reinforced with ceramic fibers
- Titanium-aluminum alloys
- Advanced carbon-carbon composites
During this time period, commercial passenger aircraft became more common. The Ford Tri-Motor was one of the first commercial aircraft, although its interior looked very different from today’s commercial jets. The Tri-Motor’s interior was similar to a coach train car, with a center aisle and a single seat on either side.
The Boeing 307, launched in 1938, featured cabin pressurization which allowed the aircraft to fly higher than previous planes. With faster speeds and greater range, passengers were able to travel further. That’s why the Boeing 307’s airplane interior was wider and designed more for comfort, with leather seats, bathrooms and other amenities.
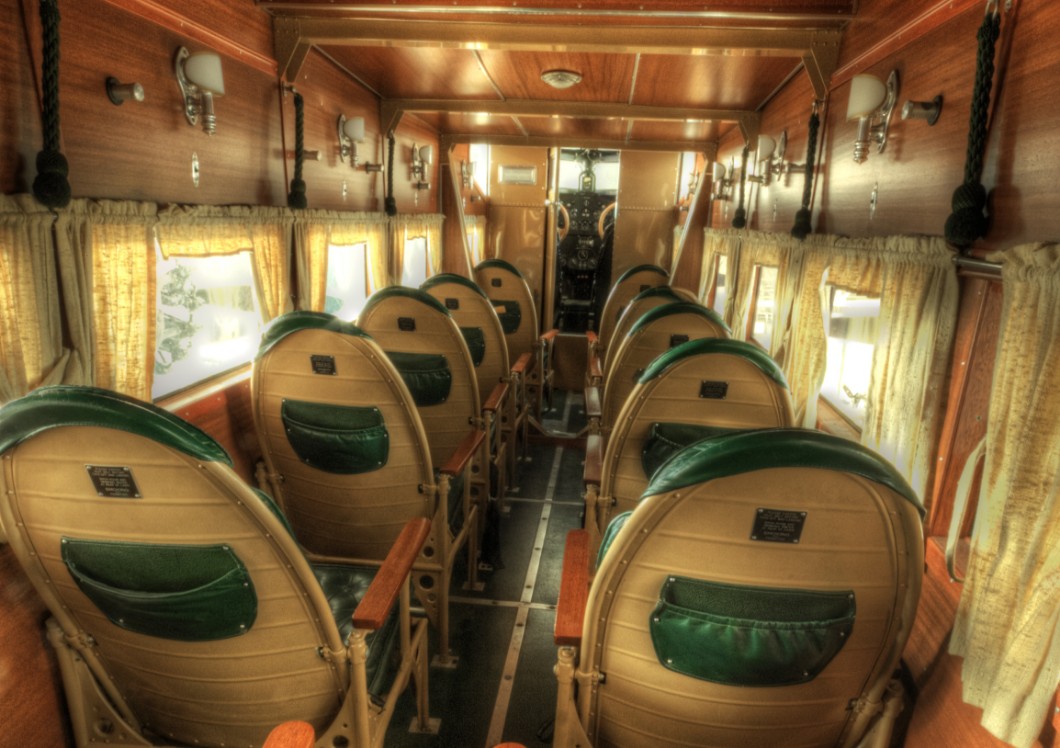
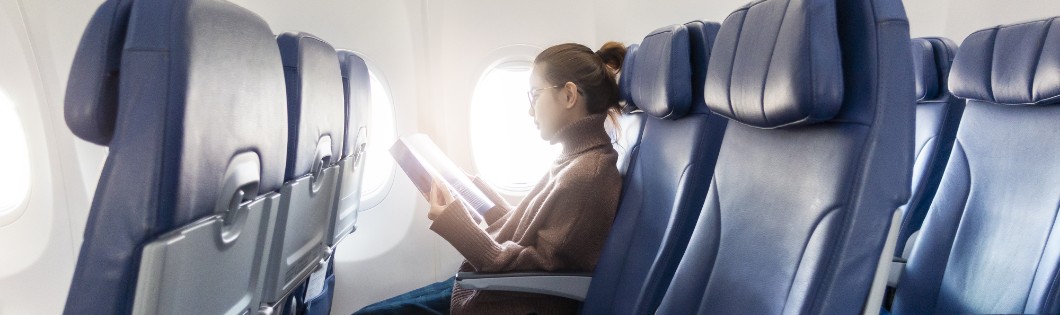
1950s to the Present: Composite Materials and Comfortable Airplane Interiors
Initially, commercial flight was a luxury for the well-to-do, and the airplane interiors represented this focus with a wide range of amenities. As commercial jetliners became more common in the 1960s, the tourist class was introduced, making flight more affordable with a stripped-down version of the interior including tighter seating conditions.
The Boeing 707 was launched in the late 1950s and looked essentially like modern jets, with rows of comfortable seats, overhead compartments, windows and other modern comforts.
In the 1980s, safety regulations for airplane interiors dramatically improved. New rules demanded airline seats be able to withstand up to 16 Gs of force, along with new fire safety rules, which resulted in manufacturers adding a fire-retardant layer on seat cushions and cabin textiles.
Modern planes are manufactured to be stronger, safer and more fuel-efficient using composite materials. Fiberglass and other fiber-reinforced resins make today’s aircraft faster and lighter. Composite materials have many benefits including:
- Lower cost
- Lightweight and strong
- Possibility of more streamlined shapes
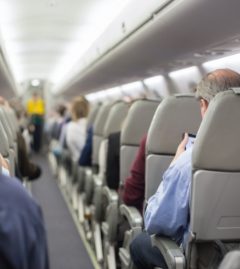
Let Duracote Provide The Airplane Interior Solutions You Need
Duracote offers a wide range of aircraft interior products to help make passengers safer and more comfortable. As one of the leading companies for airplane interior materials, we take pride in our incredibly high standards. We design products at the forefront of the next phase of the evolution of airplane interiors. Our airplane interior materials meet global performance standards and our customers’ unique specifications. Whether you need sound control, fire-retardant materials or floor coverings, Duracote has you covered.
Browse our website today and contact us to find out more about how Duracote can help.