Innovative Lightweight Materials for Aerospace Interiors
Innovative aircraft interior products that contain composites and lightweight metals are revolutionizing aviation. These materials provide exceptional strength and durability while significantly reducing weight.
Composites, for instance, combine multiple materials to achieve superior performance characteristics. Lightweight metals such as aluminum alloys offer excellent corrosion resistance and structural integrity. These advancements result in improved fuel efficiency and lower operational costs, making them indispensable in modern aviation.
- Carbon fiber composites: Known for their high strength-to-weight ratio, these materials provide significant weight savings without compromising structural integrity. They are used in various parts of the aircraft, from fuselage panels to interior components, ensuring both strength and durability.
- Aluminum alloys: These lightweight metals offer excellent corrosion resistance and structural integrity. They are widely used in aircraft frames and interior structures, providing a balance between weight reduction and durability.
- Honeycomb structures: These are engineered for enhanced structural stability with minimal weight. Used in flooring and paneling, honeycomb structures provide excellent strength and rigidity while keeping the aircraft light.
- Advanced polymers: These materials offer superior flexibility and durability, making them ideal for interior applications such as seat frames and cabin linings. They are lightweight yet strong, contributing to overall weight reduction and improved fuel efficiency.
- Titanium alloys: Known for their exceptional strength and heat resistance, titanium alloys are used in critical areas that require high durability and temperature tolerance. They are commonly found in engine components and high-stress areas of the aircraft.
The Importance of Reducing Aircraft Weight With Ultra-Lightweight Materials
Reducing the weight of an aircraft cabin significantly impacts fuel consumption and operational costs. Studies show that for every kilogram reduced in an aircraft’s weight, airlines save up to 3,000 gallons of fuel annually. This reduction leads to considerable cost savings and contributes to a decrease in carbon emissions. Innovative aircraft interior materials play a pivotal role in this process, with advanced composites, lightweight metals, and high-strength polymers being at the forefront of innovation.
Implementing these advanced materials enhances fuel efficiency and extends the aircraft’s operational lifespan by reducing wear and tear. Lightweight aircraft interior materials such as carbon fiber composites and aluminum-lithium alloys offer superior strength-to-weight ratios, making them ideal for various components within the aircraft. These materials are used extensively in flooring, cabin linings, seats, and even overhead bins, contributing to an overall weight reduction without compromising safety or comfort.
The benefits of using lightweight materials extend beyond fuel savings. By reducing the aircraft’s weight, airlines can increase payload capacity, allowing for more passengers or cargo on each flight. This improvement in operational efficiency can lead to higher revenue potential. Additionally, the use of lightweight materials reduces maintenance costs. Lighter components experience less stress and strain, resulting in a longer lifespan and fewer replacements.
The environmental benefits are substantial. Reduced fuel consumption directly translates to lower carbon emissions, supporting the aviation industry’s commitment to sustainability. With the growing emphasis on green aviation, adopting ultra-lightweight materials is becoming increasingly important for airlines aiming to meet stringent environmental regulations and improve their corporate social responsibility profiles.
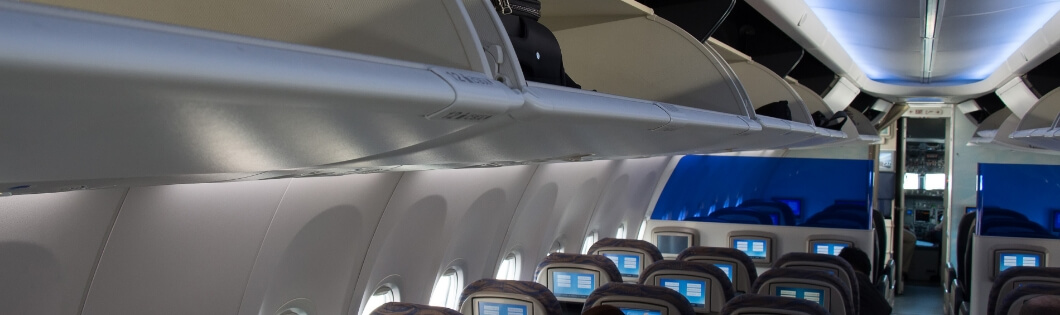
The Role of Lightweight Aircraft Interior Materials
Lightweight materials play a crucial role in aerospace interiors, being utilized in various parts of the aircraft. The applications of these materials include:
Flooring
The flooring benefits from advanced composites that provide durability while keeping weight to a minimum. These materials, such as carbon fiber-reinforced polymers, are engineered to withstand heavy foot traffic while maintaining structural integrity. By reducing the flooring weight, airlines can enhance fuel efficiency and improve the aircraft’s overall performance.
Cabin Interiors
Cabin interior wall material often includes lightweight metals like aluminum alloys and polymers that offer strength and flexibility. Aluminum alloys, known for their excellent corrosion resistance and structural integrity, are used extensively in wall panels and other structural elements. Polymers, on the other hand, provide flexibility and resilience, making them ideal for areas that require frequent maintenance or reconfiguration. These materials contribute to significant weight savings, which translates to lower fuel consumption and reduced emissions.
Lavatories and Galleys
Lavatories and galleys also incorporate these materials to maintain structural integrity without adding unnecessary weight. Honeycomb structures, often made from advanced composites, are used in these areas to provide enhanced structural stability while minimizing weight. These honeycomb panels are lightweight yet strong, making them perfect for use in partitions, doors, and other interior components that need to be both durable and lightweight.
Seats and Overhead Bins
Seats and overhead bins are other areas where lightweight materials are making a significant impact. Modern aircraft seats are designed using advanced polymers and composites that offer superior strength and comfort while reducing weight. This not only improves fuel efficiency but also enhances passenger comfort and safety. Overhead bins, made from lightweight composites, provide ample storage without adding significant weight, contributing to overall fuel savings and operational efficiency.
By implementing these innovative solutions, airlines can enhance fuel efficiency and reduce maintenance costs.
Environmental and Economic Benefits
Using ultra-lightweight materials in aircraft cabin interiors offers significant environmental and economic benefits.
- Reduced Emissions. Lighter aircraft consume less fuel, leading to reduced carbon emissions and a smaller environmental footprint.
- Fuel Savings. Economically, airlines benefit from substantial fuel savings, which can translate to lower operating costs and increased profitability.
- Sustainable Practices. The adoption of these materials also supports sustainable practices, as they often involve recyclable and eco-friendly components.
Overall, the integration of lightweight materials is a win-win for both the environment and the aviation industry.
Duracote’s Lightweight Aircraft Interior Materials
Duracote offers a range of innovative and lightweight aircraft interior products created to enhance performance and safety. Here are some of our key products:
Dura-Trim® Aviation Fire Safety
Dura-Trim® materials are engineered for advanced fire safety, meeting stringent regulatory requirements while maintaining a lightweight profile. These materials combine flexible PVC covers with woven fiberglass reinforcements, providing robust fire barriers. They are ideal for various applications within aircraft interiors, offering custom color options to fit aesthetic needs.
Dura-Sonic® Aviation Sound Control
Dura-Sonic® materials are designed to provide superior noise reduction within aircraft cabins. These insulation blankets not only help in noise abatement but also meet flame-resistant standards. Customizable to meet the specifications of major manufacturers like Boeing and Lockheed, Dura-Sonic® ensures a quieter and safer flying experience. Also, find out more about Boeing and Lockheed’s specifications and how they can affect you.
Frontier® Advanced Fire Safety
Duracote’s Frontier® product line offers lightweight, advanced fire-resistant materials for aircraft interiors, meeting FAR 25.856(a) standards. These materials provide superior fire barriers, noise reduction, and anti-static control, making them ideal for headliner laminates and fire-resistant coatings. Frontier® ensures high safety and performance with minimal impact on aircraft weight. For more details, visit Frontier Advanced Fire Safety.
These products demonstrate Duracote’s commitment to providing lightweight, high-performance materials that improve both the environmental and economic efficiency of modern aircraft. For custom solutions tailored to your specific needs, visit Duracote’s custom product solutions page.
FAQs About Lightweight Aircraft Interior Materials
Lightweight materials are transforming the aerospace interior industry. These materials offer enhanced performance and efficiency, making them essential for modern aviation. Below are some frequently asked questions about lightweight aircraft materials, providing insights into their benefits and applications.
What Are Lightweight Aircraft Materials Made Of?
Lightweight aircraft materials often include composites such as carbon fiber and advanced polymers. These materials offer high strength and low weight, making them ideal for aircraft cabin interiors. Duracote’s custom solutions ensure that these ultra-lightweight materials meet stringent industry standards.
How Do Lightweight Materials Improve Fuel Efficiency?
Lightweight aircraft interior materials lower fuel consumption by reducing the overall weight of the aircraft, leading to significant cost savings. This reduction in weight also contributes to decreased carbon emissions, promoting a more sustainable aviation industry.
Are Lightweight Materials as Durable as Traditional Materials?
Yes, aerospace materials are designed to meet rigorous safety and durability standards. They perform as well as, if not better than, traditional materials, ensuring long-term reliability and safety for aircraft cabin interiors.
What Is the Impact of Lightweight Materials on Maintenance Costs?
These materials often result in lower maintenance costs due to their enhanced durability and resistance to wear and tear. Lightweight aircraft interior materials can withstand harsh conditions, reducing the frequency of repairs and replacements.
Can Lightweight Materials Be Customized for Different Applications?
Absolutely. Duracote specializes in developing custom solutions to meet specific requirements in aerospace interiors. Our expertise ensures that cabin materials are tailored to various applications, enhancing both functionality and aesthetics.
What Are the Environmental Benefits of Using Lightweight Materials?
Using ultra-lightweight materials in aircraft cabin interiors reduces fuel consumption and carbon emissions. This contributes to a greener aviation industry and helps companies meet their sustainability goals.
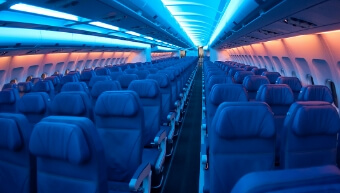
Transform Your Aircraft With Duracote’s Solutions
Discover the full potential of lightweight aircraft interior materials by exploring Duracote’s innovative solutions. Our advanced products offer unmatched performance and sustainability benefits. Contact us today to learn more or to discuss custom solutions tailored to your specific needs. Together, we can revolutionize the future of aviation.